一般的电容(capacitor)在发生微破裂(micro crack)的时候大多会产生开路的现象,并造成绝缘阻抗(IR, Insulation Resistance)升高的问题,可是多层陶瓷电容(MLCC)在终端使用者手上发生微破裂时,却常见其绝缘阻抗变小,产生漏电流(current leakage)的短路现象,归咎其原因可能是由于其层状的叠构在破裂时发生层与层之间短路的现象所造成。
如果你对MLCC的结构还不是很清楚,建议你先参考188金宝搏苹果下载 前面已经发表过【介绍多层陶瓷电容(MLCC)结构及制程】的一文。
下面我们就来谈谈一般「多层陶瓷电容」发生微破裂的可能原因。
大致上可以将MLCC破裂原因分成下列三大方向:
(这些题材大多是网路上收集来的,因为公司最近有碰到一些电容的问题,所以文章内容并非原创,内文也大量引用了网路上已经有的一些资料,如果有发现错误或不妥的地方,欢迎指正。)
- 热冲击破裂失效(Thermal shock)
- 扭曲破裂失效(Extrinsic Defect, Overstress Failure)
- 材料失效破裂(Intrinsic Defect)
热冲击(Thermal Shock)失效原理:
当零件周遭的温度升降太过急促时会形成所谓的「热冲击现象」,比如说在波峰焊(wave soldering)、回流焊(reflow)、人工焊接(touch-up)、或修復(repair)时都会快速的施加高温于材料上。而多层陶瓷电容(MLCC)在生产制造时,会使用多种不同的相容材料,这些材料会因为其各自不同的材料特性,而有不同的热膨胀系数(CTE)及导热率,当这些不同的材料同时存在于一颗电容的内部且温度急速变化时,就会形成不同比率的体积改变并互相推挤与拉扯,最后造成破裂(crack)的现象。
这种破裂往往从结构最脆弱的地方,或是结构应力最集中的地方开始发生,一般会发生在接近外露端接合中央陶瓷介面的地方,或是可以产生最大机械张力的地方(一般在晶体最坚硬的四个角落)。
而热冲击所造成的不良现象可能有下列几种:
1.形状如指甲状或U型的裂纹。
2.隐藏在电容内部的小裂纹。
3.从裸露在外的中央部份或是中央陶瓷端与外露端接合介面处的下半部开始破裂,然后随着温度转变,或是于后面的组装进行中,顺着扭曲而蔓延开来。
第一种破裂形状如指甲或U字型的裂纹与第二种隐藏在内部的微裂纹,两者的区别只是后者所受到的张力较小,而导致的裂纹较轻微而已,第一种裂纹较为明显,一般可以在金相中测出,而第二种只有当发展到一定程度后金相才可以检测出来。
(註:「金相」(metallographic)指的是金属在高倍显微镜下所呈现出来的结构影像)
扭曲破裂(overstress)、应力造成的失效原理:
扭曲破裂通常是由于外力(extrinsic)所造成,这种情形一般发生在SMT或是整机产品的组装过程当中,其可能原因有下面几种:
1.贴片机(pick & place machine)抓取零件不当造成破裂。当SMT贴片机进行取放零件时,其定中爪(centering jaw)因为磨损、对位不准确、或倾斜等原因造成抓取不稳。定中爪集中起来的压力,会造成很大的压力或切断力,继而形成破裂点。这样的破裂现象一般为可见的表面裂缝,或2至3个电极间的内部破裂;表面破裂一般会沿着最强的压力线及陶瓷位移的方向。现在的新型SMT机器已经不再使用这种定中爪设计机构了。
2.电容在贴装过程中,如果快速贴片机的吸嘴取零件或是摆放零件时压力过大,或是吸嘴(nozzle)机构发生弹簧卡死导致缓冲失效、行程错误,有可能发生零件弯曲变形导致裂纹产生。这种破裂一般会在零件的表面形成一个圆形或是半月形的压痕,并且带有不圆滑的边缘。而这个半月形或圆形的裂缝直径也会跟吸嘴的大小相同。另一种因为拉力而造成的破裂,也可能由吸嘴头所造成的损坏,裂缝会由组件中央的一边延展到另一边,这些裂缝可能会蔓延到组件的另一面,其粗糙的裂痕可能会导致电容器的底部破损。
3.对应的成对焊垫(land-pattern)布局(layout)时尺寸不均匀(包含一个焊垫接了大面积的铜箔,,另一个焊垫没有),或是印刷时锡膏不对称,也容易在经过迴焊炉(Reflow oven)时受到不同的热膨胀作用力,使单侧受到较大的拉力或推力而举起,以致造成裂纹。
4. 焊接过程的热冲击以及焊接后的基板弯曲变形,也容易导致裂纹产生。
-
4.1 电容在进行波峰焊时,预热温度、时间不足或焊接时温度过高,也容易导致裂纹产生。
-
4.2 在手工焊接(Touch-up)过程中,烙铁头(soldering iron)直接与电容本体接触,造成局部过热,或是施加压力过大,也容易导致裂纹产生。
-
4.3 焊接完成后经过分板/裁版、ICT`或FVT测试时使用针床施压不当或是整机组装时受力不均导致基板弯曲,也容易导致裂纹产生。
在机械力作用下板材弯曲变形时,陶瓷的活动范围受端位及焊点限制,破裂就会形成在陶瓷的端接界面外处,这种破裂会从形成的位置开始,从45度角向端接蔓延开来。
扭曲破裂失效。SMT阶段导致的破裂失效中,如果破裂较轻微,一般无法由金相中检测出来。SMT之后生产阶段所导致的破裂扭曲失效,金相一定可以检测出来。
MLCC材料失效破裂
MLCC的材料失效一般又分为三大类不良,这类失效通常来自电容内部的失效,而且都足以损害产品可靠性 (reliability),这类问题通常是起因于MLCC的制程或其材料选用不当所引起。
1. 电极间失效及结合线破裂(Delamination)。
这类不良通常会形成较大的裂缝。其主要原因是因为陶瓷的高空隙,或介电质层与相对电极间存在空隙所引起,使得电极间的电介质层裂开,造成潜在的漏电危机。
2. 孔洞(Voiding)。
孔洞一般发生于相邻的两片内电极之间,有时候甚至会大到多片电极,这类不良常常会引发电极间的短路并发生漏电流现象。当大空隙产生时也可能影响并降低其电容值。
这类不良的原因通常来自MLCC的制程控管不当,比如说陶瓷电容粉末有异物污染或是烧结不良所形成。
3. 燃烧破裂(Firing crack)。
燃烧破裂的开裂方向会与电极(electrodes)垂直,且大部分会从电极边缘(electrode edge)或终端开裂。
这类缺陷通常都会造成过量的漏电流(current leakage),并损害到组件的可靠性。
这类破裂的原因大多由于MLCC制造过程冷却过快所造成。
结论:
由热冲击所造成的破裂会由电容的表面蔓延到组件内部。而过大的机械张力所引起的破裂,则可由组件表面或内部形成,这些破裂均会以近乎45度角的方向蔓延。至于原材料失效,则会带来与内部电极垂直或平行的方向破裂。
另外,热冲击破裂一般由一个端接蔓延到零一个端接,由取放机器所造成的破裂,在端接下面会出现多个破裂点;因电路板扭曲而造成的损坏,通常只有一个破裂点。
延伸阅读:
显示器周围的缓冲橡胶垫片设计
COG(Chip On Glass)作业流程及注意事项
陶瓷电容(MLCC)落下后破裂并掉落分析(应力)
MLCC陶瓷电容焊接端点尺寸与电容破裂的影响性
初探HSC(HeatSeal Connector)与ACF(Anisotropic Conductive Film)制程
贊助商广告
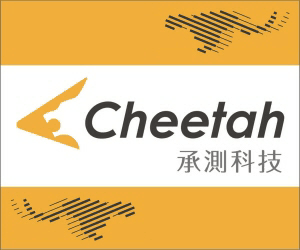
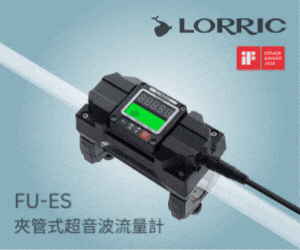
PayPal
欧付宝

Hi 你好, 请教一个问题, 现在我们有些成品已经出货, 在市场端发现接近0.1%的不开机, 经FA都是MLCC(同一颗,但是在M/B的位置不同)失效引起, 有寄到原厂分析, 都是同一个原因, 外力导致crack,现在客户要求针对成品做sorting来降低这个市场退货率, 请问针对这一现象要如何sorting? Burn-In? 还是有其他更有效的方法?
Reply
Rainbow,
首先,你是否已经知晓MLCC破裂的原因为何?MLCC原厂说的外力造成破裂是否已被证实?外力从何而来?外力是否持续存在?外力是否会持续破坏MLCC?这会关系到你sorting是否有效,如果外力会持续作用及破坏MLCC,那你sorting完的MLCC依然会持续破裂,除非你换较强壮的MLCC或做补强设计变更,否则sorting是无效的。
除非你们已经确认这是MLCC的品质问题,那Sorting才是有效的动作,比如只是某家MLCC有问题,其他供应商没有问题,或只是某家MLCC的某个批号有问题。
个人经验,我们一般对MLCC的sorting採用放大镜或显微镜目检,检查有无裂痕,但目检总有疏漏,如果可以的话,同一片板子要分次检查两次以上。MLCC电测只能测出已经裂开到影响电性的板子,对于微裂的MLCC电测是测不出来的。
Reply
熊大你好,
关于扭曲破裂(overstress)、应力造成的失效原理:
4.焊接过程的热冲击以及焊接后的基板弯曲变形,也容易导致裂纹产生。
下方有两个图示,因没叙述成因,请问我的理解是否有误
一个为Foece↑裂痕由下往上->基板弯曲变形应力造成
一个为Foece↓裂痕由上往下->贴片Nozzle下压应力造成
Reply
熊大,
很抱歉,或许我表达的不够清楚
发生破裂的电容两端PAD是一样大小,但左侧连接大面积铺铜,右侧只有PAD范围铺铜。
电容未手焊,但左侧铺铜处有需手焊的PIN约5支。
发生问题的是1206规格的电容,AOI及人工检视均未检出,检视后才进行手焊PIN作业。
破裂的位置发生在右侧端子以 “/” 的方式成整齐切面裂开,更奇怪的是裂开后出现如墓碑效应的情况,电容约成25度角上仰。
理论上如此明显的不良状况如果在手焊PIN阶段发生,作业者应当会发现;但发现电容破裂是已制作完成后由品管检出。
由于迴焊炉设定的降温斜率约1.5左右,可能当下未发生墓碑效应,但已对该电容产生一定的作用力,在后续作业或搬运的过程中才裂开。
以上是小弟愚见。
小弟入行未满一年,拜读您的文章受益良多,曾遇过的问题几乎都能从您的文章中理出头绪,唯此例现象着实奇怪,不得不请您指点。
Reply
Rain,
因为没有实际看过不良现象与PCBA的状况,所以以下言论仅是猜测。
一般墓碑零件两端有不同的铺铜大小时,小铜箔会先融锡而且先固化,因为吸热及散热较快,大铜箔因为被绿漆覆盖所以吸热及散热都会比较慢,先融锡的一端会产生较大的内聚力,并拉扯零件,如果另一端的拉力不足时就会造成墓碑。熔融锡膏固化时也是小铜箔会先固化。如果电容两端熔融锡膏固化时间差异太大,有可能形成应力,但这个还牵扯到锡膏量与防焊开窗面积与电容的可焊面积与零件摆放位置,所以不一定那边的拉力会比较大。如果担心是因为墓碑应力造成的破裂,可以试着稍微调整一下profile或尝试选用不同厂家的电容,都有机会可以改善问题。
如果可以,建议在手焊前电测检查一批电容,确认没有破裂了再手焊,以层别电容破裂是在reflow造成还是手焊时造成。
电容破裂的最大原因是应力,应力的最大来源为板弯,除非电容本身材质的CTE差异太大,否则热应力与焊接应力对现在的电容影响应该都不高了,如果拿到比较差的电容厂家例外。
Reply
熊大,
想请教您是否有相关经验。
若PCB LAYOUT无法避免MLCC一边连接大面积铜箔,而另一边只有单点铜箔的情况,是否可使用热阻焊垫的设计方式来降低MLCC破裂机率?
或者您有更佳的解决方案可提供参考?
谢谢
Reply
Rain,
Sorry! 没有这样的案例可以给你参考。
一般这种情形比较容易发生墓碑效应。
MLCC破裂的可能性很多,但是比较少是因为SMT吃锡不均造成,吃锡会造成破裂大多发生在手焊接段,因为烙铁单边焊锡在电容两端的力量难以控制。
Reply
NPO规范的MLCC仅泡水就产生裂纹不知道188金宝搏苹果下载 有没有遇过@@
Reply
Ann,
没见过,建议找原供应商问看看。
Reply
好的,谢谢~~
Reply
我司最近有一客诉高达3%,经分析发现 MLCC电容 0805 短路问题。
电容拿出来后用显微镜看发现有破裂和烧焦痕迹;无法判断这是热冲击破裂还是Overstress Failure??
能否把照片寄给188金宝搏苹果下载 帮忙看看?
Reply
Jimmy,
建议你应该把你的问题应该送给MLCC供应商分析给答案。
大部分MLCC送给厂商分析后都是硬例外题。
知道问题是一回事,如何避免又是另外一回事。
如果不想给MLCC供应商,可以送去外面的LAB做切片分析应该就会知道是什么原因造成了。
Reply
感谢版主明晰的解说。
现在了解高温的直接影响尚不如因高温产生PCB变形(间接影响)对陶瓷电容产生crack影响大。
确实发现某些PCB中段微往上翘1~2mm(长约310mm),这种变形能作为推测当时冷却时残留应力的依据吗? 或者说若无变形的PCB就没有冷却时残留应力的问题?
希望不会问太多没营养的问题。
谢谢!
Reply
Calvin,
其实还蛮担心误导你的分析,因为我并没有你的亲身经歷,一切都只是依据你的说明判断,所以给出的答案请当作参考就好,还是得自己去验证。
MLCC会破裂,不敢说100%,但至少95% 以上都是应力所造成,所以之前才会建议你把不良品送回电容厂做分析,一般可以给出可能的应力来源及方向。
板子弯曲只是MLCC破裂的可能原因之一,这之中还得看板子弯曲的位置是否刚好影响到MLCC,另一个可能就是整机组装后的应力,如果板子已经弯曲,放到机壳内就会在被强迫弯回原来的位置,就是形成应力,但这又与板子的厚度、强度(Tg)有关,所以我很难直接回答你的问题。
还有组装的应力可以用strain-gauge来量测,但似乎会做这个量测的人不多。
Reply
“半年之中连续发生超过10件1210 MLCC(10u/50V)烧毁问题,…”
经SMT厂提供资讯发现 reflow peak temperature (240~260 degree) 约有40秒。而电容原厂的reflow temperature 要求最多20秒。
有下列问题请教:
1. 是否可判断这是电容(短路)烧毁问题的主要原因?
2. 是否会影响其他正常电容的寿命?
3. 如果SMT厂 reflow peak temperature (240~260 degree) 改成20秒 是否会产生其他的问题?
谢谢!
感恩
Reply
Calvin,
基本上240~260˚C用了40秒,确实有点长,一般都要求高于220˚C的时间落在30~60秒,而高于250˚C以上基本在10秒内。不过这只是参考值,各家工厂的参数不太一样,还得以零件特性而定,最重要的时要所有零件都可以吃锡还不会烧坏。
以MLCC来说,温度太高烧坏到很少听到,比较有可能是高温造成板子变形,冷却后残留应力造成MLCC破裂后造成烧毁。这个应该可以请MLCC厂商帮忙分析下烧毁的原因。
Reply
我司在半年之中连续发生超过10件1210 MLCC(10u/50V)烧毁问题, 发生概率高时会达1%. 之前生产数年均无此现象,并可排除电路设计及PCB layout的问题.
不知是否可请 188金宝搏苹果下载 先生当做专案,帮忙分析. 敬候回覆.
谢谢!
Reply
calvin,
上班族,领人薪水,想先把自己份内的事做好,所以个人不接案例,因为要花很多心力先去瞭解制程与设计,也抽不出时间~
印象中好像有专门的顾问公司可以做分析,但没有实际接触过。
Reply
你好,
我们遇到了电容漏电问题,可是很奇怪的现象是温度越高,漏电越严重(在工作温度内。)。电容阻抗会掉到几百K程度,回到常温又会恢復正常,温度一升高漏电又开始变严重。但是,用3百多度的烙铁一碰它,它就恢復正常不再漏电。这也是一种Crack 不良吗?
另外,MLCC 如果我想自己研磨,要如何判定研磨的方向呢?不然磨错边就看不到层的结构了。
谢谢!
Reply
一般的MLCC如果有漏电通常是crack。
切片的时候通常都是磨长边。
Reply
我有将不良图片邮件给您,请帮忙分析下,盼復.谢谢!
Reply
Sumin;
Sorry没有收到照片。请使用部落格右上角的电子邮件图示寄送电子邮件。
Reply
目前我正在为我遇到的问题头疼,看了你的阔论后理解了一些,但是我这边还有一个与你提到的现象不一样,那就是在电极与本体间有碎裂的现象,是不是材料的问题引起?
Reply
Sumin;
光看你这样的描述无法了解你的状况,最好有图片可以参考。
Reply
熊大:
如果螺丝锁的位置靠近陶瓷电容。而且塑胶壳的锁付螺丝的柱子已经干涉到焊点。会不会因为锁螺丝的扭力造成破裂。如何测试呢
Reply
Hi,
想问一个问题,就是你们工厂对于研发的好的产品是否都有DVT的测试,测试项和标准是根据什么来的,最近碰到一些问题,有没有一些文档可以供参考的。
Reply
FA;
我们的产品基本上都会做EVT,DVT的测试。
每家公司的产品测试项目都会不一样,基本上会有摔落、ESD、EMI、环测…等,另外还会再加一些自己产品的特殊需求。比如Micro-USB connector的插拔实验。
Reply
忽然想到,以前遇到跟原厂的FAE 聊的时候,尤其是新FAE对电容制程一知半解的时候,他们都说 前辈说:裂横的(与电容PAD垂直,也就是熊大上方电极失效的照片)咻修(受热影响,太热或热冲击),裂直的、拢ㄟ(撞的)。原厂太部份是这样来做初步的判定 ,后续再展开现场的环境确认 。
Reply
莺歌狼;
有时候还真的得有实作经验才能说服客户。
裂横的是 咻耶 造成的。
裂直的是 拢丢 造成的。
也的确可以大概含括大部份的破裂问题。
Reply
在贴装过程中,如果贴片机的吸嘴取零件或是摆放零件时压力过大,就有可能发生零件弯曲变形导致裂纹产生。
以前有做过实验 故意将零件厚度写少0.3mm 这样压力过大 chip c并无裂纹产生 因为通常nozzle的上方机构有弹簧可吸震 当然smt机器大不同 须问原厂的弹簧的行程有多大
当然这是指健康的chip c
也有拿原材不良 就是过将零件不置件 手放过reflow就发生crack 拿来以上面的条件打 是真的会因压力过大在reflow前发现有凹陷
Reply
paul;
这真是经验之谈。
我认为SMT的机器一直推陈出新,有些旧有的问题厂商都会想办法克服,但PCBA的制造工厂还是存在很多旧的设备,或是维修时的不小心,所以还是把机器造成凹陷的问题放在这里,让大家可以参考。
Reply
aha….自己都不小心有笔误了,,,touch up
Reply
熊大,万分感情你的分享!!
上面有个笔误了,
迴流焊(Wave soldering) –》 reflow soldering
以上的现象只有在touch up中遇到比较多,其他的暂时没有遇到过,因为从事这行才两年。
Reply
JiuCheng;
Thanks抓错,已经订正好了。
Reply