【8D report】是电子组装业界蛮常使用的『问题分析与对策解决』的工具之一,因为其执行步骤有条理且清楚易懂,所以【8D report】通常被用在回覆客户的投诉案件报告上。
所谓【8D】指的是【8 Disciplines process (八个纪律作业程序)】的简称。填表者基本上只要依照事先设定好的步骤依序按部就班执行,就可以帮助大部分的品管人员一步一步的找出问题发生的原因,还可以让你向客户解释整个问题是如何被发现或发生的,你又是如何分析问题并找到问题发生的真正原因(root cause),又是如何验证问题是否真正解决,採取了那些预防措施来防止问题继续发生,并避免未来发生类似的问题。
其实【8D report】跟【QC Story】及DMAIC非常的相似,只是名称上有点不同罢了,基本精神其实是一样的,都是建立一套系统并依照一定的逻辑顺序来帮助使用者釐清问题并加以解决,还可以留下纪录提供日后的参考。
【8D report】的样式其实非常多,但基本上方法大同小异,只要抓到其节奏及重点就可以了,下面188金宝搏苹果下载 就【8D report】的内容大致说明,因篇幅有限,如果去品质学会上课可能得花5~6个钟头,本文只是约略讲解其精神:
Discipline 1. Form the Team
D1-第一步骤: 建立问题解决小组。
想要解决问题通常都得跨部门、跨单位,以电子组装厂为例,一般来说解决问题小组的基本成员应包含下列人员,当然可以视需要找其他部门的人来参与。
-
品管部(Quality Assurance):通常是小组召集人,负责统一回答客户的问题。
-
制程部(process):负责找出制程当中哪里可能有问题。
-
测试部(Testing):寻找为何无法藉由测试方法检测出有问题的产品。
-
生产部(Production):配合工程师的要求,作实验或是收集数据,以利问题的发现并协助执行解决方案。
Discipline 2. Describe the Problem
D2-第二步骤: 描述问题。
建议要善加运用5W1H (Who, What, Where, When, Why, How) 描述,来向团队说明问题是在何时、何地、发生了什麽事、严重程度、目前状态、如何紧急处理。
如果可以的话要尽量展示问题发生当时的相关照片和目前所收集到的迹证。可以把自己比拟为CSI犯罪现场的鑑识人员,将所有的证物及细节描述的越清楚,团队就能越快的进入状况,解决问题的速度也会越快。
另外,如果可以事先准备好产品的流程图(Flow Chart)来解说,也可以帮助一些可能对制程不是那么熟悉的团队成员更快进入情况并了解问题点。
Discipline 3. Contain the Problem
D3-第三步骤: 暂时性对策。
当问题发生时,不论真因是否已经找到,都必须要先止血,所以会先採取一些必要的暂时性措施(temporary solution)。比如说如何在客户端帮忙筛选(Screen, Sort)出有问题的产品,或者是更换良品给客户,让客户可以继续生产或是顺利出货。
在制造端应该要先採取措施来防止友问题产品继续发生或出货到客户的手上,例如更换机器生产、加严筛选、全检、将自动改爲手动、库存清查等等动作。
暂时对策决定后,应立刻交由团队成员带回执行,并随时回报成效。
Discipline 4. Identify the Root Cause
D4-第四步骤: 找出问题真正原因。
188金宝搏苹果下载 发现很多朋友几乎都卡在这一关,虽然这是【8D Report】中最难的部份,但还是有许多的品管手法可以运用,帮助我们更有系统的发现问题,寻找真因。
最常使用的方法是【要因分析图(鱼骨图)】,它提醒我们有哪些线索可以寻找,就人(员)、工(制程)、(来)料、机(器)、量(测)、及环(境)等六个面向,逐项检讨找出问题可能发生的原因,仔细比较、分析问题发生前后变动的状况,比如说人员是否变动?作业手法是否更动?厂商来料是否变更?治具是否更换?跟环境的温度、溼度是否相关?
另外,也要都加使用【柏拉图】来收集并分析最应该优先解决的问题点。
经验告诉我们,日常作业的资料收集越是齐全的工厂,找到真正问题的速度就越快,例如有日常修理报表,Cpk(统计制程),良率即时通报系统..等。也可以运用『实验计画(plan experiment)』法找出最佳制程。
也有人用【原因树(Why tree)】,依照工程经验,一路追踪问题发生的最根本原因。
相关阅读:SPC(统计制程管制)、Cpk、制程能力之解说与整理
Discipline 5. Formulate and Verify Corrective Actions
D5-第五步骤: 选择永久对策。
找到造成问题的主要原因后,即可开始拟出对策与方法。对策也许会有好几种,例如修理或更新模具。最好对这些候选的对策列出其优缺点,要花多少钱?多少人力?能持续多久?再从这些方法中选择最佳对策并执行,还要确认这些对策不会産生其他副作用。
也可以利用类似FMEA的评分来决定对策的执行优先顺序。
Discipline 6. Correct the Problem and Confirm the Effects
D6-第六步骤: 执行及验证永久对策。
当永久对策准备妥当,确认有效后就可以停止暂时对策,而且还要对永久对策作验证。请注意,验证工作非常重要,最好可以模拟、重制(duplicate)问题发生的现象,才算是真正找到问题的主因。
比如说IC的脚损伤,是因为模具损伤所造成的,更换好的模具上去问题就解决了,这时要重新再把有问题的模具装上,确定这套模具还会重复同样的不良现象,这样才算是完成验证,如果重新装回原来的模具,不良现象也没有出现,可能原因就不一定出在模具,必须重新寻找主因。
Discipline 7. Prevent the Problem
D7-第七步骤: 防止类似问题再发生。
其他类似还有在生产的产品虽然尚未发生同样的问题,亦需作同步的永久对策改善,防止问题在工厂内再度发生,通常有ISO认证的工厂,必须透过一定程序把永久对策标准化,比如说更改作业指导书,或是规定于标准作业程序(SOP, Standard Operation Procedure)中。
Discipline 8. Congratulate the Team
D8-第八步骤: 感谢团队。
对那些努力付出解决问题的团员给予嘉勉,使其产生工作上的成就感,并极乐意解决下次碰到的问题。
这里有个8D报告的实际案例可以参考一下:
《到底【8D report】该如何写,才不会老是被客户退件?》
其他参考文章:
8D report写不出来怎么办?8D报告为何这么难写?
延伸阅读:
QC story品质改善歷程
六个标准差(six sigma)运用于日常生活
118bet网址多少
介绍品质工程师(QC/QA)在工厂的角色与职责
介绍「制程工程师」及「产品工程师」在公司的角色
贊助商广告
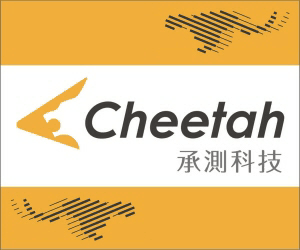
PayPal
欧付宝

感谢精短了解8D
Reply
我们大陆厂这阵子遇到的难题,在D4这关就卡住,缺乏懂得收集数据,分析错误的技巧偏弱。连鱼骨图都做不好..导致一份错误分析报告2个月的时间还无法交出具体成果。
以下是关于D4的一些分析工具 (刚好前阵子刚受PLM,8D的培训..)
Flow diagram(适合针对process,流程分析使用)
Histogram 直方图(分析数量,失误的频率等)
Ishikawa 鱼骨图(提出可能的错误原因,可以搭配5个为什么方法进行探讨)
IST/IST NICHT 是非是实判断(针对是系统性的方式,判别一件事实..但我个人觉得太难使用了..不知是不是跟德国人的思考逻辑有关 XD)
Reply
德莉雅,
的确,我这里也有发现D4似乎是很多朋友的罩门,除了你列出来的那些分析方法外,其实还有Why-Tree,不过最重要的是要有逻辑观念。
Reply
有幸看到这么棒的网志,感谢前辈无私的分享经验!谢谢
Reply
由于业务单位不清楚什么是 CpK; 我身为品质部主管有义务要对业务介绍; 但讲太理论他们会听不懂或听不下去. 所以不知站长是否有 CpK 的 presentation.
BR
Dawang
Reply
我自己没有准备这样Presentation的slide耶!Sorry 啰!
抓了一份大陆网站的资料寄给你,你看看合不合用,简体版本,不能用就删了吧!
另外,部落格内有许多关于Cpk 的文章也可以参考一下,大部分应该都很浅显:
//m.letratesoro.com/tag/cpk/
Reply
版主
想不到在这边可以找到能依循的模式,谢谢.请问PCB内层同心圆,如在铆合时发现搭线,这是代表板子的涨缩问题,还是沖孔机的问题,如果预铆时X-RAY发现搭线可以压合作业吗?是否代表板内内容物已经短路?
王金龙
Reply
很实用的文章!!公司的产品出问题,根本不知道怎么找原因
想不到在这边可以找到能依循的模式
太感谢了!!
Reply
其实每个步骤都很重要啦!比如说问题的描述如果不清楚,就会误导后续的步骤,不可不慎…
Reply
分享一下我看过的8D (D3~D7)
D3: develop containment action
D4: define and verify root cause
D5: choose and verify permanent corrective action for root cause
D6: implement and validate permanent corrective action
D7: prevent recurrence
D4 D7 个人以为难度较高
Reply
有幸看到这么棒的网志,感谢前辈无私的分享经验
Reply
内容写实且实用,一定花了不少时间完成,非常不错,感谢您的分享,请继续加油!
Reply
写文章花时间是一定的,只要有人欣赏就算有所收穫了!
Reply
希望有机会听您好好的讲解一下。并可以分享您的经验!
Reply
不错的网志,继续加油啊!
Reply
谢谢!
Reply