公司最近在做一个新的专案,RD对板子Layout的要求是越来严苛,因为板子越做越小,连带的对防焊(Solder Mask)尺寸的要求也相对的缩小,可是厂商的制程能力又跟不上来,有能力的说要加价(cost up),一听到要加钱,所有人都开始缩手,继续沿用现有PCB板厂的制程,其结果就是防焊层印刷偏移超出了焊垫/焊盘。
防焊层印刷偏移会造成什么问题呢?
如果是BGA的焊垫/焊盘偏移,就会造成BGA锡球的焊垫变小,最后造成焊锡短路(solder short),怎么焊垫变小反而会造成短路呢?原来钢板(stencil)上的开口是固定的,也就是钢板上同一个开口的锡膏量理论上是固定的,如果每片电路板BGA的焊垫大小都一致,钢板可以根据实际的焊垫大小来给予适当的开口大小与锡膏量,但如果不同批电路板,有的焊垫维持在原来的尺寸,可是有的板子焊垫却缩小了,可是锡膏量还是维持一样,就会变成锡膏过多造成溢流(overflow)的现象,严重时就会溢流到邻近的焊垫,形成焊锡短路。
可是焊垫(焊盘)怎么会变小呢?
这就好像戴头套只露出两个眼睛的道理是类似的,如果头套没有套到正确位置,稍微给它偏了一点点,眼睛就会被头套给盖到,遮住了半颗眼睛。眼睛可以想像成「焊垫」,而防焊层就是「头套」了。或许有人文章看到现在还搞不太清楚,所以在啰唆一下,这防焊层(Solder Mask)就是绿漆啦!明白没!再不明白,那就把板子拿出来看看那一大片的绿色就是啦!这些绿漆会覆盖住电路板上不需要露出来的铜箔及线路,以避免不必要的接触短路或氧化。(註:有些板子的防焊会印成黑色、红色,但大部分都是绿色)
因为188金宝搏苹果下载 公司的新电路板设计把防焊层的公差抓在+/-1mil(+/-0.0254mm),可是板厂防焊层的制程能力为+/-2mils(+/-0.05mm),于是实际印刷偏差的防焊层就覆盖到原来该露出来焊垫,让原本该露出来焊垫变小,于是问题产生了以上的问题。另外一个原因是我们为了防止HIP发生,所以将BGA外圈的锡膏量印得比较多,所以发生短路的焊垫几乎都集中在BGA的外圈锡球。(相关阅读:如何解决BGA锡球的HIP(Head-In-Pillow)虚焊问题)
下图显示电路板BGA下面的防焊层印刷偏移,造成焊垫大小不一致。 | 下图显示其他零件的防焊层印刷偏移,造成焊垫大小不一的现象。 |
![]() |
![]() |
下图显示BGA因为焊垫变小,造成锡膏过多而最终形成焊接短路的结果。
接下来的解决办法:
1. 要求板厂局部修改有问题焊垫的防焊层开孔位置及尺寸,原则上要求BGA下面的所有焊垫大小要趋向一致。
2. 重开钢板(stencil)把容易发生短路的BGA外圈焊垫开口缩小,以便降低锡膏印刷量。
延伸阅读:
增加锡膏量可以改善BGA焊接不良?
如何从设计端强化BGA以防止其焊点开裂?
如何设计加强产品的BGA焊垫强度以防止BGA开裂(SolderMask Defined, SMD)
贊助商广告
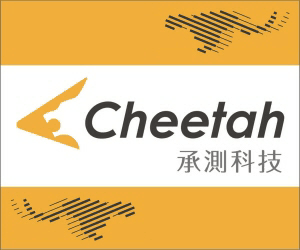
PayPal
欧付宝

PCB一直存在材料涨缩问题,再加上Solder Mask用的曝光光罩(mask)本身也有涨缩与对位偏移问题,楼主提的第一个解决办法实务上很难做到。好消息是,国外已有厂商开发出次世代的Solder Mask Coater可大幅改善偏移问题,但这种机器何时能被板厂广泛採用仍是未知数。
Reply
银河漂流;
谢谢您所提供的意见与讯息,关于改善对策第一点,目前两家板厂的防焊都已经控制在要求的偏移量内,至于焊如果改善并没有详细追踪,有可能用挑的,或是用更精准的设备,总之目前生产已经都符合要求了。
Reply