SMT产线为何要分长短线?其主要目的当然是为了要提高效率,这里的长短线指的是SMT线体的长度,也就是机台的数量,大家应该都有看过零件不到10颗的板子吧!像这种板子就可以使用短线SMT来作业,只要一台锡膏印刷机+一台贴片机+回焊炉就可以搞定。甚至连SPI及AOI都不一定需要。而长线SMT通常会放置比较多台的置件/贴片机(pick and placement machine),适合单面零件数比较多的板子。
那SMT产线要如何提升效率?
188金宝搏苹果下载 这里提供两个思考的方向给大家参考
一、line balance(生产线平衡)
就是要尽量保持让每一台SMT设备都处在运转中没有待机。
我们以有一条有3个作业员的包装流水线来说明好了,假设原先作业的制程安排,
第一个作业员的作业时间为30秒,
第二个作业员的作业时间为20秒,
第三个作业员的作业时间为10秒,
不考虑其他因素造成的工时损失,那么产出基本为每30秒可以完成一个包装,大家觉得这样的安排有没有什么不合理的地方?就是第3个作业员大部分时间都在等待没事干,而第1个作业员却得一直做没得休息。如果我们可以把第1个作业员的工作分一点给第3个作业员,让两个作业员的时间平均都变成20s,理论上三个作业员的时间就会通通是30s,而产出的时间也可以从30s降为20s,也就不会出现有作业员忙得命,而有些作业员则很轻松的现象。
而SMT产线的配置也是一样的道理,因为SMT线是由好几台不同设备所组成的产线,我们只要合理的分配每个设备的生产时间,也就是将零件合理的分配到不同的贴片机,让每台设备的生产时间都非常接近,基本上就可以达到最佳的生产效率,否则一台那么贵的SMT设备却经常处于待机状态,就是在烧钱。
二、使用「拼板(panelization)」
拼板就是将许多的单板拼凑在一起成为一片比较大的板子,比如说我们常常会说2合1(2in1)或3合1(3in1)甚至更多合1的板子就是拼板。使用拼板最直接的优点就是可以减少取放的时间,因为一次就可以同时拿取多片板子,而拼板最大得优点则是可以提升SMT的生产效率,这个我们文章后面会再说明。
但是有优点就会有缺点,在我们要将PCBA组装进去成品的机壳以前必须要再额外做裁板(de-panel)的动作,将拼板变回成一片片单独的板子,所以有人会质疑为何要先拼板后裁板,这是因为拼板的好处远比额外裁板作业的利益还要多出很多,所以现行作业里几乎所有的板子都会做拼板。这就有点像明明每天都要把衣服脱掉,为什么每天都还要穿衣服。
SMT产线的瓶颈通常会出现在那一站?
可能很多人不晓得,SMT产线的瓶颈一般最常出现在「锡膏印刷作业」,这是因为其他各站的作业时间长短几乎都是依照零件数量来决定的,但是锡膏印刷的时间则是依照板子大小来决定,使用钢板印刷一次锡膏的时间大约需要20~30秒,而且时间几乎是固定的,很难再缩减,但是其他各站的时间我们只要把需要贴片的零件数量增加上来,大多能超过20秒以上,所以才会说SMT的瓶颈通常出现在锡膏印刷。
那要如何增加零件的数量呢?这时候拼板的优点就显现出来了,假设单一片板子上的零件数量有100颗好了,把它做成4in1的板子是不是就变成了400颗。零件数增加了,每台SMT设备贴片的时间自然也就跟着增加了。如果单一面板子上的零件数或样式不够多,在情况允许的情况下也可以考虑正反面颠倒的阴阳拼板(mirror board)。
延伸阅读:
PCB採用「阴阳板」拼板的好处
决定PCB的连板拼板数量时应该考虑的几个因素
SMT採用「阴阳拼板」或「鸳鸯拼板」使用上的限制
贊助商广告
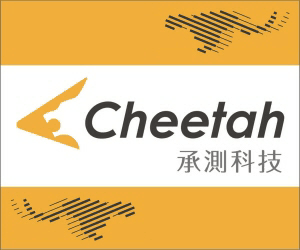
PayPal
欧付宝

188金宝搏苹果下载
感谢您的回覆,我目前在系统厂任职,不过常有许多跟欧美客户学习的机会,真空回焊炉在现今算是挺夯的设备,刚好HELLER & ERSA我都接触过,现在的成本可能比想像中的低,C/D通常是30%起跳。
大家抢来抢去的,我认为Voids依IPC-A-610的标准是过于松散了,这也是几个月前,欧美客户在3D AXI前巡厂跟我叮咛的事项。
这边非常感谢188金宝搏苹果下载 这十几年的指导,生产费用的确是一个大问题,如何做好成本预算的考量是大课题,小弟有幸参与了几个大专案,心得感想是:产品能往高阶走,就不要往低阶靠,唯有一直跟着技术前端走,维持品质,才能累积更多知识,消费者自然会买单。
以下是我Study Voids的参考资料,这边分享给被气泡问题困扰的各位:
References
[1] Robert Bosch GmbH ,Udo Welzel, Norbert Holle “ Voids in SMT Solder Joints – Trends in Automotive Electronics” Schwieberdingen, Germany , 2021.
[2]T. Ewald, N. Holle and K.-J. Wolter, “Void formation during reflow soldering,” in IEEE 62nd Electronic and Technology Conference, San Diego, CA, USA, 2012.
[3]N. Holle, T. Ewald and U. Welzel, “Voids in SMT Solder Joints – Myths Revisited,” in IPC APEX EXPO Proceedings, San Diego, 2018.
Reply
188金宝搏苹果下载 您好,我目前在业界负责汽车电子的生产,我分享一下我NPI工作遇到的一些心得。
以2023年来说,产线现在通常都走高度自动化,SMT产线的瓶颈现在通常都在「真空回流焊炉」&「3D AXI」,而它们的主要的问题,就是因为安全保护程序过多,而导致UPH(Units Per Hour)通常会跟不上其他设备。
关于拼板,现在很多都走双轨,并用Carrier拆装的方式增加产能,比起以前斤斤计较板材利用率,现在更多购置设备就直接加大真空腔体,双轨、扩大可容纳最大单板尺寸。
※未来半导体的双层载具制程有可能会导入电子产品生产,目前还没有太多系统厂敢尝试。
而大线拆小线,这边分享了一下我的专案遇到的问题以及会考虑拆线的考量点。
通常会拆小线是因为
a) 产品sku多、方便转换工单,柔性较高
b) 方便Ramp up爬坡,减少设备损耗年限
c) 方便做copy line,佔地面积较小
d) NPI阶段线体投入成本较低
e) 可利用其他小线做DOE(Design Of Experiment),制程会比较好运用
但会遇到问题
a) SMT设备昂贵,很难大线拆小线(ex.炉子、3D光学检测设备)
b) Coating涂覆也很难大线拆小线,反而一个大线更好
c) 购置第一条小线的价格可能会跟第三条线成本差距大(折扣也难谈)
d) 为避免线体间成品有差异,可能要使用Online-SPC实时管控
Reply
特斯拉,
先感谢你的经验分享。感觉上你的经验比较像是自己的工厂,否则就是大咖的汽车电子厂了。
虽然进入2023年,但是业界使用真空回焊炉的比率仍不是很高,就像你说的以汽车、军事或安全相关的行业居多,因为这些行业对焊锡气泡/空洞的要求比较高。另外,检查设备越多,卡关的机率就越高,当然这得视制程的稳定度而定。
至于双轨回焊炉,比较适合用在板子上零件差异不大的板子,而且双轨对回焊炉的功率要求也很高,热补偿效率必须足够,而且CoCo也必须多,手机板倒是看到有人使用。
SMT引入半导体制程应该是趋势,但也进限于高阶或特殊产品,不会全面引进,因为生产费用卡在那哩。其实,一些PCB产业也在引进半导体制程,因为载板的线路要求越来越窄,成品要求也越来越小,但一样在有限的未来,这只是少数高阶产品会使用。
Reply